Single axis robot positioner TS-X/TS-P
Single-axis robot positioner TS series, providing easy operation, excellent functions, and low price.
![]() |
TS-X・TS-P Operating method : I/O point tracing / Remote command |
Feature
1. Design that allows a clean installation
Unified installation sizes
Height and installation pitch are unified throughout the series. Units can be installed neatly within the control board.
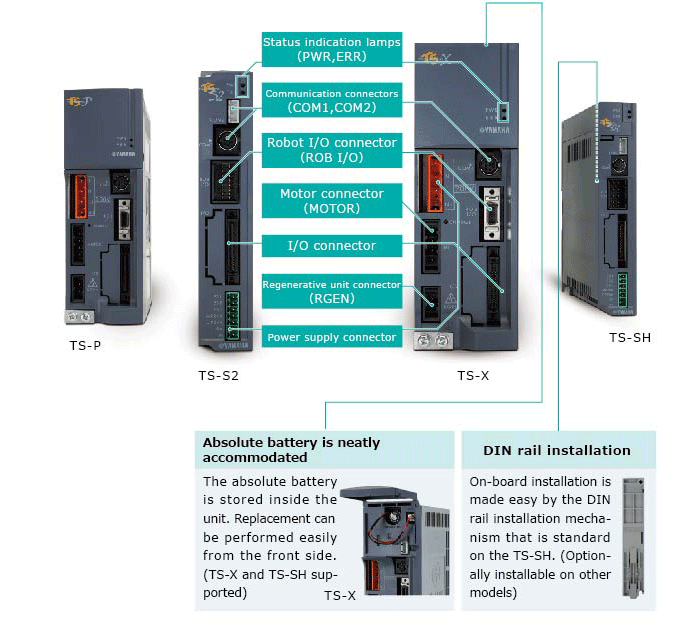
2. Selectable I/O interfaces
Two RS-232C ports provided
Connect support tools : Intuitive operation supports controller design and maintenance. Daisy-chaining : Two ports can be used to daisy-chain up to 16 units. Communication commands : Easily understood ASCII text strings can be used to perform robot operations. |
![]() |
Selectable 100V/200V
The TS-X/P let you select AC100/200V as the power input. (The 20A model is 200V only.)
The TS-S2/SH is DC24V input.
A variety of I/O interfaces
In addition to NPN and PNP, you can choose CC-Link, DeviceNetTM, EtherNet/IPTM, and PROFINET field networks.
Positioner interface
Functionality has been condensed into an I/O interface with 16 inputs and 16 outputs. In addition to easy positioning, this also includes functionality that enhances interoperability with the control device.
Remote commands
Numerical data can be directly manipulated by using the four-word input and four-word output areas. You can add new direct positioning commands to further unify the data at the control device.
Gateway function
new types of connection are provided to reduce network costs. (CCLink, EtherNet/IPTM, and PROFINET are supported.)
3. Positional interface
"Positioner function" for easy positioning
You can easily perform positioning operations by specifying the number of a point that is registered in the data, and entering a start command.
A variety of output functions
The TS controller provides a variety of status outputs that are linked with positioning operations. By selecting and using an output appropriate for the scene, this can contribute to cost-saving measures such as making the steps of the control device's program more efficient or by reducing the peripheral equipment.
Consecutive operation, linked operation
By specifying a branch destination, it is possible to execute positioning operations consecutively. Additionally, by specifying linked operation, operation with the branch destination can be executed while changing the speed without positioning stops; this allows control programming to be simplified and takt to be shortened.
Jog and point teaching functions are provided as standard
Jog movement and point teaching functions are provided as standard for input signals. By linking these with buttons of a touch panel etc., a simple teaching system can be constructed.
4. Remote commands
Ideal for unifying data management
Remote commands are functions by which the control device can directly handle data such as points and parameters using the word area of the field network. Numerical data can be operated directly by using the word area. This promotes unification of data management.
5. "Gateway function" -- a new way to connect
Decrease network cost
One controller equipped with a field network board can provide unified management of up to four I/O interfaces via a daisy-chain connection. This allows network cost to be decreased while enabling the same type of I/O control as when one board is installed for each unit. (CC-Link and EtherNet/IPTM are supported)
No need to connect or disconnect cables during operation (up to 16 units)
From a single PC, handy terminal, or touch-panel display, it is possible to specify point data and parameters, perform operations, and monitor the status for up to 16 axes on daisy-chained controllers. For everything from design to maintenance, a connection to only the first controller is sufficient; any desired controller can be accessed simply by switching the station number, without having to connect or disconnect cables.
Communication commands
An easily handled command protocol using ASCII text strings supports a wide range of needs from data editing to operation and status monitoring. By daisy-chaining multiple devices, simple multi-axis control can be performed.
7. "KEYENCE PROTOCOL STUDIO Lite" serial communication settings software
By loading a TS settings file into PROTOCOL STUDIO Lite, communication settings and main communication commands can be registered automatically. Ladder-less data editing and daisy-chaining can be easily accomplished.
Daisy-chain connections (up to 16 axes)
Communication with the KV-L21V uses a Yamaha-made communication cable (D-sub type). By using daisy-chain connections, up to 16 axes can be managed together.
Automatic device assignment for each communication command
If the communication type is specified as cyclic, the desired information to be obtained is automatically stored in data memory.
8. Touch operator interface "Pro-Face" GP4000 Series
Connecting GP4000 Series made by Pro-face to Robot Positioner, TS-S2, TS-SH, TS-X, TS-P enables you to use a lot of functions as well as basic operations on Touch Operator Interface.
Can easily check a state and change settings.
-Check the status (the current position, speed etc)
-Basic operations such as Jog operation, inching operation, return to origin, error reset etc.
-Set, edit, or back up point data and parameters
-Check triggered alarms and detailed descriptions of alarm history
Supports 3 languages
Supports Japanese, English, and Chinese (simplified, traditional)
Specifications
Model | TS-X / TS-P | |||||
100V AC input | 200V AC input | |||||
Basic specifications | ||||||
Driver model | TS-X105 / TS-P105 | TS-X110 / TS-P110 | TS-X205 / TS-P205 | TS-X210 / TS-P210 | TS-X220 / TS-P220 | |
Number of controllable axes | Single-axis | |||||
Controllable robots | TS-X: Single-axis robot FLIP-X series TS-P: Linear motor single-axis robot PHASER series | |||||
Power capacity | 400VA | 600VA | 400VA | 600VA | 1400VA | |
Dimensions | W58 × H162 × D131mm | W70 × H162 × D131mm | ||||
Weight | Approx. 0.9kg | Approx. 1.1kg | ||||
Input power supply | Control power supply | Single phase AC100 to 115V +/-10% 50/60Hz | Single phase AC200 to 230V +/-10% 50/60Hz | |||
Motor power supply | Single phase AC100 to 115V +/-10% 50/60Hz | Single phase AC200 to 230V +/-10% 50/60Hz | ||||
Axis control | ||||||
Control method | Closed loop vector control method | |||||
Operating method | I/O point tracing (Positioning operation by specifying point number) / Remote command | |||||
Operation types | Positioning, merge-positioning, push, and jog operations | |||||
Position detection method | TS-X: Resolver with multi-rotation absolute function TS-P: Magnetic type linear scale | |||||
Resolution | TS-X: 16384 pulses/rev. or 20480 pulses/rev. depending on the robot TS-P: 1µm | |||||
Origin search method | TS-X: Absolute / Incremental TS-P: Incremental / Semi-absolute | |||||
Points | ||||||
Number of points | 255 points | |||||
Point type setting | (1) Standard setting:Set speed and acceleration in percent of the respective maximum settings. (2) Custom setting: Set speed and acceleration in SI units. |
|||||
Point teaching method | Manual data input (coordinates input) , Teaching, Direct teaching | |||||
External input/output | ||||||
I/O interface | Selectable from the following: NPN, PNP, CC-Link, DeviceNetTM, EtherNet/IPTM, PROFINET | |||||
Input | Servo ON (SERVO), reset (RESET), start (START), interlock (/LOCK) origin search (ORG), manual mode (MANUAL), jog motion - (JOG-), jog motion + (JOG+), Point number selection (PIN0 to PIN7) | |||||
Output | Servo status (SRV-S), alarm (/ALM), operation end (END), operation in-progress (BUSY), control outputs (OUT0 to 3), Point number output 0 to 7 (POUT0 to POUT7) | |||||
External communications | RS-232C 1CH | |||||
Power supply for brake | DC24V +/-10% 300mA (prepared by the customer) | |||||
Safety circuit | Emergency stop input, main power input ready output, emergency stop contact output (1 system: When the HT1 is used.) | |||||
Options | ||||||
Handy terminal | HT1, HT1-D (with enable switch) | |||||
Support software for PC | TS-Manager | |||||
General specifications | ||||||
Operating temperature / Operating humidity | 0°C to 40°C, 35% to 85%RH (non-condensing) | |||||
Storage temperature / Storage humidity | -10°C to 65°C, 10% to 85%RH (non-condensing) | |||||
Atmosphere | Indoor location not exposed to direct sunlight. No corrosive , flammable gases, oil mist, or dust particles | |||||
Anti-vibration | All XYZ directions 10 to 57Hz unidirectional amplitude 0.075mm 57 to 150Hz 9.8m/s^2 | |||||
Protective functions | Position detection error, power module error, temperature error, overload, overvoltage, low voltage, excessive position deviation, overcurrent, motor current error | |||||
Protective structure | IP20 |
Catalog
-TS-S/TS-X/TS-P Catalog Spec (850 KB)
-[TS-S/TS-X/TS-P] basic specifications (182 KB)
-[TS-S/TS-X/TS-P] part names / dimensions (214 KB)
-Data overview (158 KB)
-Point data (158 KB)
-NPN type input / output wiring diagram (131 KB)
-I/O circuit details (131 KB)
-Emergency stop circuit example (131 KB)
-I/O Specifications (131 KB)
-TS-X / TS-P specification selection table (214 KB)
-Regenerative unit RGT/RGU-2 (274 KB)
-Ordering method (182 KB)
-Accessories (380 KB)