Robot positioner TS-S2
TS-S2 is positioned type controller that only performs point trace. Simple operation only by specifying point number data
![]() |
TS-S2 -Operating method : I/O point tracing / Remote command |
Feature
1. Available for all TRANSERVO series models.
2. Main operation patterns
3. Detailed data can be set for each point
Settings such as acceleration, deceleration, zone output range, and position margin zone can be set for each point. Different operations can be easily specified by combining these settings with the above operation patterns.
Setting items | ||
Setting item | Description | |
1 | Run type | Specifies operation pattern such as ABS, INC, positioning, push, and point-to-point link. |
2 | Position | Specifies position or distance to move. |
3 | Speed | Specifies maximum speed during operation. |
4 | Accel. | Specifies acceleration during operation. |
5 | Decel. | Specifies deceleration during operation (Percentage of acceleration) |
6 | Push | Specifies motor current limitation during pushing operation. |
7 | Zone (−) | Specifies upper and lower limits of "personal zone" for each point data. |
8 | Zone (+) | |
9 | Near width | Specifies position margin zone where "near width" output should turn on. |
10 | Jump | Specifies next movement destination after positioning or linked destination for point-to-point operation. |
11 | Flag | Specifies stop mode and others. |
*Acceleration and deceleration can be set in easy-to-understand percentage (%) units (standard setup) or in SI units (custom setup) which make it easy to calculate the cycle time.
4. Maximum acceleration auto setting
Acceleration is a critical parameter that determines how long the robot can continue operating (or service life). In worst cases, setting the acceleration too high may cause the robot to breakdown after a short time.
On the TS series, the maximum acceleration is finely set by taking into account the service life span of the motor output and the guide for each robot model and payload. This eliminates any worry about setting the acceleration too high by mistake.
5. Applicable to EtherNet/IP.
Select from the following I/O types to match the host controller specifications. All hardware is built into the positioner unit so cabling and wire hookups are easy.
Item | Description |
---|---|
NPN | Input: 16 points, 24VDC +/- 10%, 5.1mA/point, positive common Output: 16 points, 24VDC +/- 10%, 50mA/point, sink type |
PNP | Input: 16 points, 24VDC +/- 10%, 5.1mA/point, negative common Output: 16 points, 24VDC +/- 10%, 50mA/point, source type |
CC-Link | Supports CC-Link Ver. 1.10, remote device station (1 station) |
DeviceNet | DeviceNet slave node |
EtherNet/IP* | EtherNet/IP adapter (2 port) |
6. Up to 16 controllers can be connected. (Daisy chain function)
As the TS series controllers are connected through the daisy chain, the data designing or monitoring of a desired controller can be made through one personal computer or handy terminal.
Since the daisy chain is applicable to not only "TS-S2" and "TS-SD" dedicated to the TRANSERVO, but also "TS-X" and "TS-P" applicable to higher-grade models, it can be connected to all YAMAHA single axis robots. This is very convenient when many more robots are used.
*"TS-SD" cannot use the HT1 and touch panel display "Pro-face".
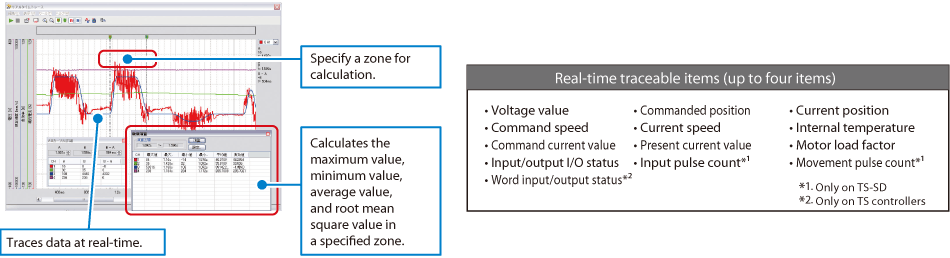
Various monitor functions and detailed error logs
Operation simulation
Specifications
Model | TS-S2 | |
Basic Specification | ||
Number of controllable axes | Single-axis | |
Controllable robots | TRANSERVO series (ALL models) | |
Power capacity | 70 to 110VA | |
Dimensions | W30 x H162 x D82mm | |
Weight | Αρρrox. 0.2Kg | |
Input power supply | Control power supply | DC24V +/-10% maximum |
Motor power supply | DC24V +/-10% maximum | |
Axis control | ||
Control method | Closed loop vector control method | |
Operating method | I/O point tracing (Positioning operation by specifying point number) / Remote command | |
Operation types | Positioning, merge-positioning, push, and jog operations | |
Position detection method | Resolver | |
Resolution | 4096P/rev, 20480 P/rew* | |
Origin search method | Incremental | |
Points | ||
Points | 255 points | |
Point type setting | (1) Standard setting: Set speed and acceleration in percent of the respective maximum settings. (2) Custom setting: Set speed and acceleration in SI units. |
|
Point teaching method | Manual data input (coordinates input), Teaching, Direct teaching | |
External input/output | ||
I/O interface | Selectable from the following: NPN, PNP, CC-Link, DeviceNet, EtherNet/IP** | |
Pulse train command input | - | |
- | ||
Input | Servo ON (SERVO), reset (RESET), start (START), interlock (/LOCK) origin search (ORG), manual mode (MANUAL), jog motion - (JOG-), jog motion + (JOG+), Point number selection (PINO to PIN7) | |
Output | Servo status (SRV-S), alarm (/ALM), operation end (END), operation in-progress (BUSY), control outputs (OUTO to 3), Point number output 0 to 7 (POUTO to POUT7) | |
External communications | RS-232C 1CH | |
Safety circuit | Emergency stop input, emergency stop contact output (1 system: When the HT1 is used.) | |
Options | ||
Handy terminal | HT1, HT1-D (with enable switch) | |
Support software for PC | TS-Manager | |
General specifications | ||
Operating temperature / Operating humidity | 0°C to 40°C, 35% to 85%RH (non-condensing) | |
Storage temperature / Storage humidity | -10°C to 65°C, 10% to 85%RH (non-condensing) | |
Atmosphere | Indoor location not exposed to direct sunlight. No corrosive, flammable gases, oil mist, or dust particles | |
Anti-vibration | All XYZ directions 10 to 57Hz unidirectional amplitude 0.075mm 57 to 150Hz 9.8m/s^2 | |
Protective functions | Positioning detection error, power module error, temperature abnormality, overload, overvoltage, low voltage, gross position error |
*Resolution is different each model.
**EtherNet/IP will be supported from August, 2013.
Catalog
-Basic specifications (192 KB)
-Dimensions (301 KB)
-Input/Output specifications (214 KB)